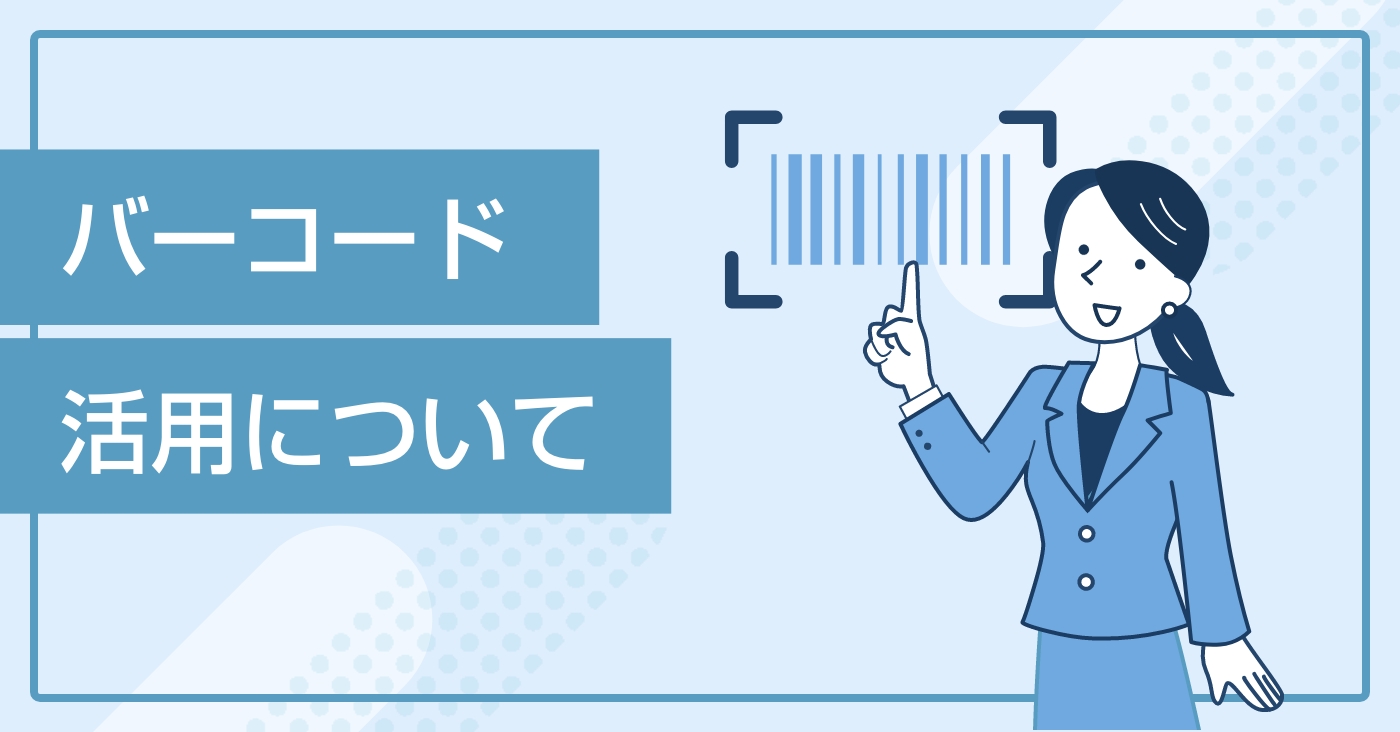
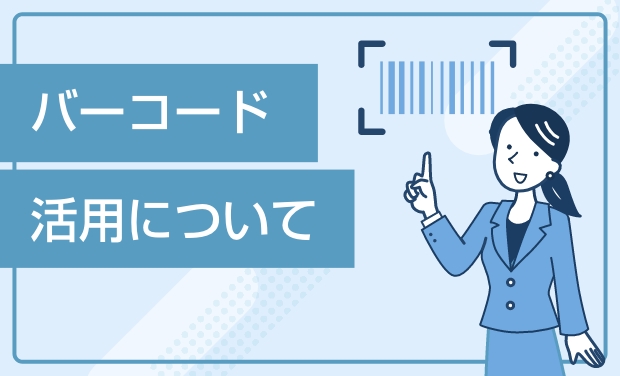
製造現場での記録業務において、従来の紙やエクセルを使った方法に限界を感じている方は多いのではないでしょうか?
効率的にミスなく生産管理を行いたいのであれば、バーコード活用は必須です。
この記事では、生産管理でバーコードを活用するメリットや具体的な用途、活用事例について解説します。
製造現場でのバーコード活用について
製造現場では、一つの製品を製造する過程で、最適な品質管理や原価管理、納期管理が必要なため、膨大な記録業務が発生します。
そんな中、紙帳票への手書き入力や、エクセルで手入力を都度行うのは、非常に非効率的であり、記録漏れやミスも頻繁に発生します。
そんな製造現場が抱える課題に対する解決策としては、バーコード活用がおすすめです。
なぜなら、バーコードを活用すれば、製造指示番号や品番、工程情報などを、一つの工程が完了したタイミングで、
ハンディターミナルで読み込み、簡単に生産実績を記録することが出来るからです。
これにより、記録業務の手間を軽減することが出来ます。
バーコード活用のメリット
バーコードを活用するメリットは、実は記録業務の手間を軽減するだけではありません。
その他にも、以下のようなメリットがあるので、ご参考下さい。
人為的ミスの削減
紙やエクセルでの記録は、書き間違いや見間違いなどが発生するため、人為的ミスが発生することが多いです。
しかし、バーコードを活用することで、記録する情報が少なくなる為、ミス発生を抑制することが出来ます。
また、生産管理システムによっては、出荷時に間違った製品のバーコードを読み取るとエラーを出す機能や、
生産時に間違った部品を使おうとするとエラーを出す機能などもあるため、記録業務で発生するミス以外にも様々なミスを削減することが可能です。
転記や集計といった工数の削減
紙の帳票に記録する場合、後でエクセルやシステムに転記したり、集計する必要があります。
しかし、記録情報が大量にある場合、相当な工数がかかるため、企業によっては事務担当者を雇ったり、管理者が遅くまで残業しているケースが多いです。
バーコード活用により、システムに直接記録出来ると、それまでかかっていた工数が大幅に削減出来るため、
その他のより価値の高い業務に工数を割り当てることで、現場全体の生産性向上につなげることが出来ます。
現場状況をリアルタイムで把握可能
なんらかのトラブルが発生し、素早く対応しなければ納期が遅延してしまうような場合、
紙の帳票やエクセルで手入力していると、現場の状況把握に時間がかかります。
その他にも、使用する原材料や部品の在庫が少なくなった場合、素早く対応出来なければ在庫不足を引き起こしてしまうでしょう。
しかし、バーコード活用により、システムに直接記録ができていれば、生産状況や在庫状況をリアルタイムで瞬時に把握することが出来、素早く対応することが出来ます。
最適な生産管理を行う為には、リアルタイムで状況を把握することが重要です。
バーコード活用のデメリット
これまで様々なメリットについて紹介してきましたが、デメリットについても把握しておくことが重要です。
デメリットを把握した上で、導入することで、トラブル発生時の対処方法についても素早く判断することが出来ます。
コストが発生する
当たり前ですが、バーコードで管理するためには、専用端末やシステムの導入が必要になるため、一定の初期費用が掛かります。
また、サーバー維持や保守管理などにもコストがかかります。
お金をかけたにもかかわらず、既存のシステムに対応していない、業務になじまないといったリスクを避けるようにしましょう。
体制整備が必要
バーコードの導入に合わせて、現場の業務フローを見直す必要があります。
例えば、読み取り手順やエラー発生時の対処方法などです。
その為、導入時に合わせて、従業員研修やマニュアル作成など、運用体制を整備する必要が出てきます。
正確に読み取れない場合もある
バーコードに汚れや傷が付いてしまうことで、正確に読み取れなかったり、読み取りにくい場合も時には発生してきます。
印字不良などの不具合が発生する場合もあるため、バーコードラベルの発行時に印字の品質チェック等も行うことを推奨します。
バーコード活用で実現できること
次にバーコードを活用することで実現できることを具体的に3つ紹介します。
製造業は業種や生産方式によって、様々な生産管理が行われており、それによって抱える課題も様々な為、
自社の課題に合わせて、バーコードを活用すべきか否かを判断しましょう。
在庫管理の手間削減
取り扱っている部品などが多いメーカーなどでは、在庫の種類が膨大な量になり、管理する手間が掛かります。
・気付かない間に在庫が無くなっていて組立出来ない
・どこに何の部品が合るのか把握出来ていない
上記のような、課題を抱えている企業も多いのではないでしょうか?
そんなときにバーコードが活用出来れば、記録漏れや人為的ミスを削減出来るため、リアルタイムかつ正確な在庫状況を把握することが出来ます。それにより、過剰在庫や欠品も防止しやすくなるでしょう。
在庫のロケーション管理が出来るシステムの場合、倉庫内で探し回るといった無駄な工数も削減することが出来ます。
トレーサビリティの確保
様々な業種でトレーサビリティが求められていますが、特に食品、医薬品、化粧品などの業種では、適性な品質を確保するために厳しい品質管理が求められています。しかし、どの製品にどの材料が使われているのか等を確認するためにはロット管理なども行う必要があり、
手間な作業が多くなるため、人為的ミスによる不良品発生等が起こりやすい状況です。
しかし、バーコードを活用して、事前にロットや有効期限などの情報が含まれたバーコードを発行しておくことで、
読み取り時に記録やエラーチェックを行い、人力で行うよりも早く、ミスもなくなるため、徹底した品質管理を行うことが出来るでしょう。
製造原価の正確な把握
利益率を向上させるためには、製造原価の正確な把握が重要です。
しかし、材料費や労務費などを実際に細かく管理出来ている企業は多くありません。
バーコードを活用できれば、原材料や部品をロットごとに購入金額を記録しておき、実績登録時にバーコードを読み取って、製品のロットに紐づけておけば、その製品を作るのにかかった材料費を計算することが出来ます。
また、実際の作業開始時と終了時にバーコードで読み取ることで、労務費を計算することが出来ます。
このように、バーコードを活用すれば、経費以外の原価を正確に把握することが出来るため、利益率向上のための改善施策を素早く判断することも出来ます。
まとめ
バーコードを活用するメリットやデメリット、実現できることなどについて、ご紹介しました。
製造業において、様々な課題を現場から解消することが出来るバーコードは、非常に手軽で、導入しやすい傾向もあります。
紙やエクセルでの管理中心になっていて、人為的ミスや管理の手間などに頭を悩まされている方は、
ぜひバーコードの活用を検討してはいかがでしょうか。